news
予防保全と予知保全の違いとは?食品工場における設備管理の最適解コラム
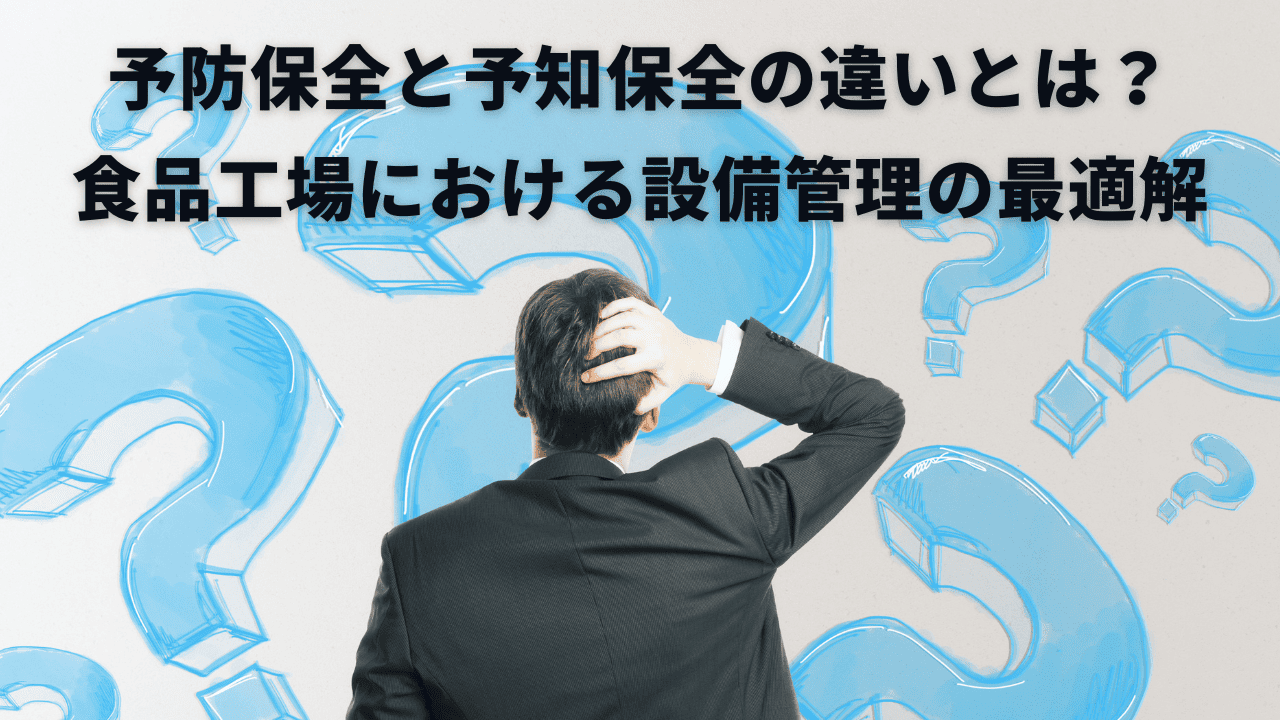
食品製造業では、安全で高品質な製品を安定的に生産するために、設備の適切な維持管理が不可欠です。その中で「予防保全」と「予知保全」という2つの保全手法が注目されています。これらの違いを理解し、自社に最適な保全戦略を導入することで、故障リスクの低減、コスト削減、生産性向上を実現できます。
本記事では、食品工場における予防保全と予知保全の違い、それぞれのメリット・デメリット、導入事例を詳しく解説します。
予防保全とは?
予防保全(Preventive Maintenance)は、設備の故障を未然に防ぐために、定期的な点検・メンテナンスを行う保全手法です。具体的には、使用時間や稼働回数を基準にしたメンテナンススケジュールを設定し、部品交換やオーバーホールを実施します。
予防保全のメリット
突発的な故障の防止
計画的にメンテナンスを実施するため、突発的な故障を減少させ、生産ラインの安定稼働を実現できます。特に、食品工場では、製造プロセスの中断が品質管理や納期に影響を与えるため、予防保全による安定稼働の確保が非常に重要です。また、故障の未然防止により、生産ロスを最小限に抑え、企業の利益確保につながります。
管理のしやすさ
点検スケジュールが明確なため、設備管理が容易になり、担当者の負担軽減につながります。特に、長期間稼働する設備では、定期的なメンテナンスを行うことで、劣化や摩耗の進行状況を把握しやすくなります。さらに、計画的な管理により、部品の調達計画を立てやすくなり、急な設備トラブルによる緊急対応を減らすことができます。
品質の安定化
設備の劣化を抑え、一定の品質を維持しやすくなります。食品工場では、製造設備の微細な変化が製品の品質に影響を及ぼすため、定期的なメンテナンスによって一貫した生産品質を維持することが不可欠です。例えば、加熱や冷却装置の温度変動が発生しないように保守を行うことで、食品の味や風味の安定性を確保することができます。また、設備の適切な調整により、エネルギー効率の向上や、無駄な廃棄物の削減にもつながります。
予防保全のデメリット
過剰なメンテナンスコスト
実際には故障しない部品も定期的に交換するため、コストがかかる場合があります。特に、必要以上のメンテナンスが発生すると、コストが増加し、利益圧迫の要因となることがあります。
計画通りに作業を進める必要がある
点検・交換作業のために設備を停止しなければならず、生産計画に影響を与えることがあります。例えば、生産がピークを迎える時期に予防保全を実施する場合、適切なタイミングでの調整が必要です。
予知保全とは?
予知保全(Predictive Maintenance)は、設備の状態をリアルタイムで監視し、異常の兆候を検知して必要なメンテナンスを行う手法です。振動センサーや温度センサー、AI解析を活用し、データに基づいて最適なタイミングでメンテナンスを実施します。
予知保全のメリット
コスト削減
必要なタイミングで部品交換を行うため、予防保全に比べて無駄なメンテナンスを減らすことができます。これにより、設備の寿命を最大限に延ばし、資源の有効活用が可能になります。特に高価な設備を扱う食品工場では、メンテナンスコストの最適化が重要な課題となります。
ダウンタイムの最小化
リアルタイムで設備の状態を監視できるため、緊急停止のリスクを軽減できます。センサーやAI解析を活用することで、異常が発生する前に適切な対応が可能になり、計画外の生産停止を防ぐことができます。また、異常の早期発見により、設備の修理コストも抑えられます。
※ダウンタイムとは?
「ダウンタイム」とは、設備や機械が稼働できない時間のことを指します。食品工場で は、生産ラインが停止してしまう時間(予定外の故障やメンテナンスによる停止時間な ど)がダウンタイムにあたります。
生産性の向上
計画的かつ最適なタイミングでのメンテナンスにより、生産ラインの稼働率を向上させることが可能です。特に食品工場では、需要の変動に対応するために柔軟な生産計画が求められますが、予知保全を導入することで設備の可用性を最大限に確保し、安定した生産を実現できます。
予知保全のデメリット
初期投資が必要
センサーやAI解析システムを導入するためのコストがかかります。特に、中小規模の食品工場では、導入費用を確保することが課題となることがあります。しかし、長期的にはメンテナンスコスト削減や生産効率向上による利益増加が見込めるため、投資対効果を十分に検討することが重要です。
データ分析の知識が必要
設備のデータを正しく活用するためには、専門的な知識やシステムの運用スキルが求められます。また、データを収集するだけでなく、適切に分析し活用するための人材教育も必要です。近年では、クラウドベースの解析ツールやAI技術の進化により、データ分析のハードルが下がりつつありますが、導入後の運用体制の整備が成功の鍵となります。
予防保全と予知保全の違い
予防保全と予知保全は、設備の維持管理の方法として異なるアプローチを持ちます。
予防保全は、一定のスケジュールに従って設備の点検や部品交換を行う手法です。例えば、半年ごとにモーターのオーバーホールを実施したり、使用時間が1万時間を超えたコンプレッサーのベルトを交換したりすることがこれに該当します。計画的にメンテナンスを行うことで、突発的な故障を防ぎやすくなりますが、実際には不要な部品交換を行ってしまう可能性もあります。
一方、予知保全は、設備の状態を常時監視し、異常の兆候が見られた場合にのみメンテナンスを実施する方法です。例えば、振動センサーを活用し、ポンプの振動レベルが基準値を超えた際に警告を出し、故障の前兆を把握したうえで部品交換を行います。これにより、無駄な交換を減らしながらも、適切なタイミングでのメンテナンスが可能になります。
どちらの保全方法を選ぶべきか?
食品工場では、以下の要因を考慮して、適切な保全方法を選択することが重要です。
コスト
初期投資を抑えたい場合は予防保全が適しています。一方で、設備の長期的な運用コストを削減し、無駄な部品交換を減らしたいなら予知保全が有効です。特に、高価な設備を扱う場合は、予知保全を活用することで、適切なタイミングでのメンテナンスが可能となり、コスト管理がしやすくなります。
生産ラインの重要度
食品工場では、24時間稼働するラインや、短時間で大量生産する設備が多くあります。こうした重要な設備には、リアルタイムの監視が可能な予知保全が適しており、突発的なトラブルを回避することで、生産ロスを最小限に抑えることができます。一方で、使用頻度が低い設備や、短期間のダウンタイムが許容される設備には、予防保全の導入が適しています。
データ活用の体制
予知保全は、センサーを活用したデータ収集やAIによる解析が必要となります。そのため、社内でデータ分析のスキルを持つ人材が確保できるか、または外部ベンダーのサポートを活用できるかが重要な判断基準になります。企業のデジタル化が進んでいる場合や、スマートファクトリー化を推進している工場では、予知保全の導入がより効果的となります。
まとめ
予防保全と予知保全は、それぞれ異なるメリット・デメリットを持ちます。食品工場では、設備の特性やコスト、技術的な要因を考慮しながら、最適な保全戦略を選ぶことが重要です。今後、AIやIoT技術の発展により、予知保全の導入がより容易になることが期待されます。例えば、AIが過去の故障データを解析し、より精度の高い異常検知が可能になることで、メンテナンスの最適化が進むでしょう。また、クラウド技術を活用することで、遠隔地からでも設備の状態をリアルタイムに監視し、適切なタイミングでメンテナンスを実施できる環境が整いつつあります。さらに、5G技術の普及により、データの高速処理が可能となり、より精密な予知保全システムが構築されることが見込まれます。これにより、食品工場における生産ラインの安定稼働が実現し、設備の長寿命化やコスト削減にも貢献できるでしょう。
今後の食品工場では、これらの先端技術を活用したスマートメンテナンスが主流となる可能性が高く、設備管理の効率化が一層進むことが予想されます。効率的な設備管理の実現により、生産性の向上とコスト削減を最大限に引き出すことができるでしょう。
FOOD TOWNでは他にも様々な食品業界に特化した内容を随時更新中です!
まずは下記から無料会員登録をお願いします!
お問合せはこちらまで
Robots Town株式会社
〒532-0011
大阪府大阪市淀川区西中島6丁目6-17 RIC1st.ビル 501号室
TEL:06-4703-3098