news
食品工場における労働災害とは?原因・事例・防止策を徹底解説コラム
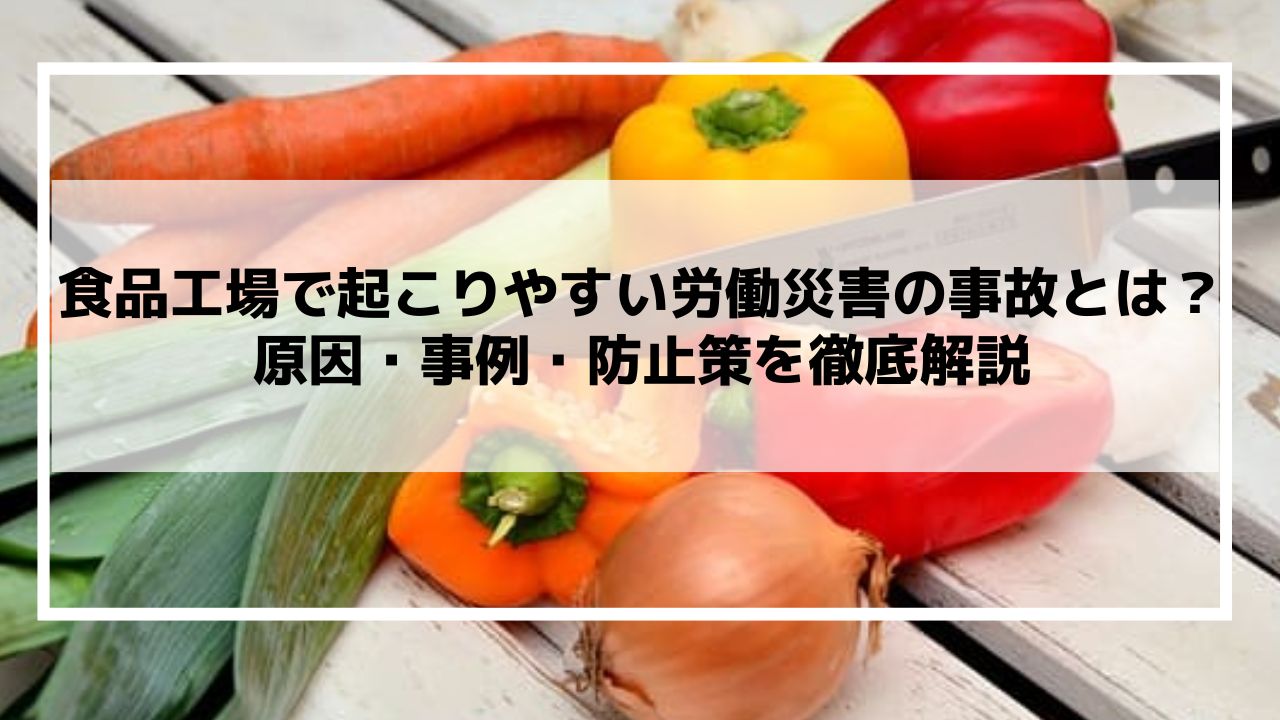
食品工場では、はさまれ事故、転倒、火傷、薬品事故などの労働災害が他業界と比べて多く発生しています。
その背景には、人手不足による無理な作業体制や、安全対策・教育の不備といった構造的な課題が存在しています。
本記事では、
- 食品工場で労働災害が発生する主な理由
- 実際に起こった労働災害の種類と具体的な事例
- 災害を防ぐための解決策・職場環境の整え方
を解説し、“事故を防ぐ食品工場づくり”に必要な視点と対策をまとめます。
食品工場で労働災害が起こる理由
安全対策・教育が不十分
多くの食品工場では、機械の安全装置未整備や作業手順の文書化不足など、安全対策の甘さが災害の温床となっています。
- 危険箇所の特定と見える化
- ヒヤリハットや事故履歴の蓄積
- 第三者チェックの導入
- 教育資料・作業手順の整備
これらに取り組むことが、リスクの低減につながります。
食品工場で起こりやすい労働災害の事故・事例
はさまれ・巻き込まれ事故
作業服の袖や手袋がローラーに巻き込まれるなどの事故が頻発しています。
安全ガードや緊急停止スイッチの設置、稼働中の清掃を禁止するなどの対策が必要です。
以下によくある事故の事例もご紹介します。
ベルトコンベアによる事故
ある食品工場で、清掃作業中に労働者の手がベルトコンベアに巻き込まれました。手袋がコンベアに引き込まれ、手が挟まれるという事故が発生しました。原因は、機械が稼働中に清掃を行っていたことと、安全装置が適切に機能していなかったことです。
プレス機による事故
別の食品工場では、プレス機を操作中に労働者の腕が挟まれる事故が発生しました。労働者が機械の調整を行っていた際に誤って操作し、プレス機が稼働したため、腕が挟まれてしまいました。原因は、機械の安全スイッチが無効になっていたことと、適切な操作手順が守られていなかったことです。
ミキサーによる事故
食品工場で、ミキサーの清掃中に労働者の袖がミキサーのシャフトに巻き込まれる事故が発生しました。袖が引き込まれ、腕が負傷しました。原因は、ミキサーの電源を切らずに清掃を行っていたことと、袖の緩い作業服を着用していたことです。
転倒事故
床の汚れや段差、濡れた床などが原因で発生する転倒事故。滑り止め靴や注意喚起サイン、排水性の高い床材の導入が効果的です。
床の清掃中の転倒事故
ある食品工場で、清掃作業中に労働者が床にこぼれた油に滑って転倒しました。この労働者は腰を強く打ち、数週間の休業を余儀なくされました。原因は、清掃中に油が拭き取られていなかったことと、適切な滑り止め靴を履いていなかったことです。
段差による転倒事故
別の工場では、労働者が製造エリアから倉庫へ移動する際に、小さな段差に足を取られ転倒しました。この労働者は足首を捻挫し、作業に復帰するまでに時間がかかりました。原因は、段差が視認しづらく、床の標識や注意喚起が不十分であったことです。
濡れた床による転倒事故
食品加工エリアで、洗浄作業中に労働者が濡れた床で滑り、膝を強打しました。この事故の原因は、作業区域に「滑りやすい」との標識がなく、また、床の乾燥が不十分であったことです。
墜落、転落の事故
高所作業や棚からの転落事故には、脚立や手すり、安全帯などの使用が不可欠です。
階段での転落事故
別の食品工場では、労働者が階段を降りる際に足を滑らせて転落しました。手すりを持っていなかったため、階段の下まで転がり落ち、頭部に重傷を負いました。原因は、階段が滑りやすい状態であり、手すりの設置が不十分であったことです。
棚からの転落事故
食品倉庫で、労働者が高い棚から商品を取ろうとしてバランスを崩し、墜落しました。この労働者は、適切な踏み台やはしごを使用せずに棚によじ登ったため、落下して負傷しました。原因は、適切な作業用具が使用されていなかったことと、高所作業の安全対策が不十分であったことです。
化学薬品による事故
食品工場では、殺虫剤、調理機器、施設清掃用の洗剤、消毒液といった様々な化学薬品を頻繁に使用しています。
これらを適切に扱うためには、正確な使用方法を守ることが重要です。また、薬品が飛散したり吸い込むリスクがある場合には、適切な保護具を着用することが求められます。
消毒剤による皮膚の火傷
ある食品工場で、労働者が高濃度の消毒剤を取り扱っている際に、手袋を着用せずに作業を行ったため、消毒剤が手に触れて皮膚の火傷を負いました。原因は、適切な防護具の未使用と、安全な取り扱い方法の不徹底です。
化学薬品の混合による有毒ガスの発生
別の工場では、労働者が異なる種類の洗浄剤を混ぜた際に、有毒なガスが発生し、労働者が吸入して呼吸困難を起こしました。この事故の原因は、化学薬品の混合に関する知識不足と、作業手順の確認不足です。
薬品の漏洩による事故
食品工場の倉庫で、薬品を保管していた容器が破損し、薬品が漏れ出しました。この漏洩に気付かなかった労働者が薬品を踏んで滑り、転倒して負傷しました。原因は、薬品の保管方法が不適切であり、定期的な点検が行われていなかったことです。
騒音の事故
騒音レベルが高い工場では、作業員の聴力損失のリスクが存在します。イヤーマフや耳栓の使用だけでなく、金属検出機に対応した耳栓の導入など、食品工場ならではの工夫も必要です。
聴力障害の発生
ある食品工場で、労働者が長時間高い騒音環境で作業を行っていた結果、聴力障害を発症しました。この労働者は耳栓や防音ヘッドセットを使用していなかったため、騒音によるダメージを直接受けてしまいました。原因は、適切な防音対策が講じられていなかったことです。
騒音による集中力低下と機械操作ミス
別の工場では、労働者が騒音環境で作業をしている最中に、集中力が低下して機械の操作ミスを犯し、手を負傷しました。騒音によって注意力が散漫になり、機械の安全操作手順を誤ってしまったことが原因です。
コミュニケーションの困難による事故
食品工場のライン作業中に、労働者同士が騒音で指示を聞き取れず、誤った作業を行ってしまいました。その結果、製品が損傷し、機械も故障するという事故が発生しました。原因は、騒音によって労働者同士のコミュニケーションがうまく取れなかったことです。
火傷の事故
火傷は、加熱された調理器具の表面に触れたり、熱い食品の取り扱い中に、熱湯や高温の油が跳ねて肌に接触することで発生します。
高い温度の鍋や調理器具を扱う際には、鍋つかみや耐熱性の保護手袋を使用することが安全策とされます。しかし、これらが水分を含んでいると、熱が伝わりやすくなり蒸気火傷のリスクが生じるため、常に乾燥させてから使用することが推奨されます。
熱湯による火傷
ある食品工場で、労働者が鍋を持ち上げた際に熱湯がこぼれ、手に火傷を負いました。この労働者は適切な防護手袋を着用しておらず、また、鍋の持ち上げ方が不適切でした。原因は、労働者の不適切な作業手順と防護具の不使用です。
蒸気による火傷
別の工場では、労働者が蒸気殺菌機を操作中に、誤って蒸気バルブを開けてしまい、顔と腕に火傷を負いました。この事故は、労働者が蒸気の取り扱い方法を十分に理解していなかったことと、安全装置が適切に機能しなかったことが原因です。
熱い油による火傷
食品工場のフライヤーで、労働者が揚げ物を取り出す際に、誤って熱い油が跳ねて顔に火傷を負いました。この事故の原因は、防護具の不使用と、適切な作業手順が守られていなかったことです。
高温・低温による事故
熱中症や凍傷を防ぐには、冷却ベストや電熱ベストの活用、適切な休憩が必要です。
高温環境による熱中症
食品工場の乾燥室で、労働者が長時間作業を行っている最中に、熱中症を発症しました。この労働者は休憩を取らずに作業を続けており、水分補給も十分に行っていませんでした。原因は、高温環境での作業管理が不十分であったことと、適切な休憩と水分補給の指導がされていなかったことです。
冷凍庫内での低体温症
ある食品工場で、労働者が冷凍庫内で長時間作業を行っていた結果、低体温症を発症しました。この労働者は適切な防寒具を着用しておらず、定期的な休憩も取っていませんでした。原因は、防寒対策の不備と作業管理の不足です。
冷凍食品の運搬中の事故
食品工場で、労働者が冷凍食品を運搬中に滑って転倒し、冷凍食品が体に接触して火傷のような損傷を負いました。この事故の原因は、運搬経路が滑りやすい状態であり、労働者が適切な履物を着用していなかったことです。
食品工場で労働災害の解決策
5S活動を徹底する
「整理・整頓・清掃・清潔・しつけ」の5S活動は、工場内の安全性と効率性を高める基本です。5S活動を職場にどう定着させるか、以下の記事で詳しく解説しています。
5S活動について詳しく書いた記事もありますのでこちらもご覧ください。
働きやすい労働環境を作る
職場の安全性は、働きやすい環境作りが基盤となっています。企業はまず、作業現場の具体的な状況を正確に理解し、従業員が円滑に業務を遂行できるような環境整備が求められます。
まとめ
食品工場では、労働災害のリスクが日常的に存在しています。
企業全体で以下の点に取り組むことが、事故の予防と持続的な生産体制につながります。
- 安全教育と5S活動の徹底
- 適切な作業環境・装備の整備
- 労働者との密なコミュニケーション
FOOD TOWNでは他にも様々な食品業界に特化した内容を随時更新中です!
さらにFOOD TOWNご利用者様ならいつでも食品工場 自動化の相談も無料でお伺いいたします!
まずは下記から無料会員登録をお願いします!
お問合せはこちらまで
Robots Town株式会社
〒532-0011
大阪府大阪市淀川区西中島6丁目6-17 RIC1st.ビル 501号室
TEL:06-4703-3098
関連リンク・資料