news
食品工場の設備保全とは?種類を解説コラム
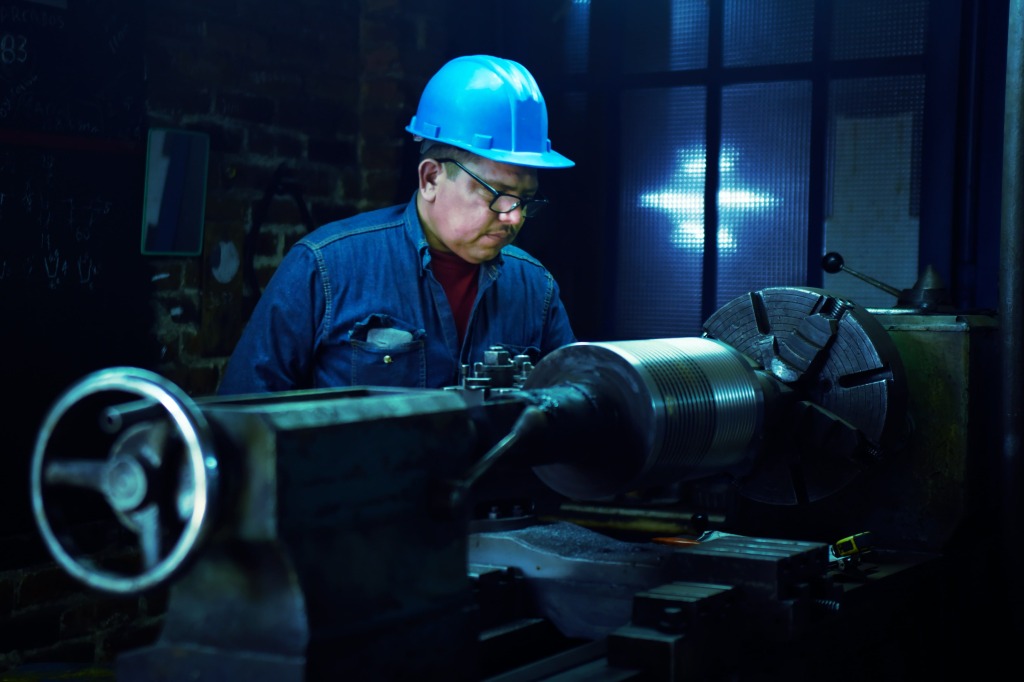
食品工場で高品質な製品を安定して生産するためには、機械や設備の維持管理としての設備保全が極めて重要です。さらに、適切なサービスを提供するためにも、設備保全は欠かせません。この記事では、食品工場における設備保全の概要、目的、課題、そして主な3つの保全の種類である「予防保全」「事後保全」「予知保全」についての情報を解説します。
設備保全とは?
設備保全とは、機械や設備の状態を把握し、工場の設備が安全・安定的な状態で稼働できるように維持していく活動のことです。企業の事業において、さまざまな設備の点検・修理を行うことで、故障を最小限に抑えることが可能です。結果として、高品質な製品の安定生産が実現します。また、設備に突発的に発生した事故など異常を発見した場合に適切な処置を実施することが大切です。
設備保全の目的
設備保全の目的は、突発的な故障を防ぎ、設備の機能を維持すること、設備の寿命を延ばすこと、そしてライフサイクルコストを削減することにあります。さらに、設備保全は安全で環境に配慮した運用を実現するためにも重要です。
1.設備機能の維持
工場内の機械や設備が正常に稼働し続けることを保証するための活動です。これにより、生産の安定性と製品の品質を確保します。
工場における機械や設備の突然の故障は、修理費用だけでなく、生産の停止による機会損失をもたらします。日常的な確認や定期的な清掃等の保全を通じて、こうした状況を防ぐために、機械や設備の定期的な保全が不可欠です。
2.設備の寿命を伸ばす
適切なメンテナンスを通じて、メーカーが設定した耐用年数を超えて、機械や設備の寿命を延ばし、設備投資の回収期間を最大化します。これにより、設備の長期的な稼働と効率的な運用が実現します。また、データを基にした保全計画の導入も、設備の信頼性を高め、環境に配慮した持続可能な運用を取得するために効果的です。
3.ライフサイクルコストの削減
設備保全を効果的に行うことは、機械や設備の購入から廃棄までにかかるライフサイクルコスト(LCC:Life Cycle Cost)を最小限に抑える事を目指します。予防的なメンテナンスによって突発的な故障を防ぐことで、修理費用や生産ロスを減少させます。
設備保全の課題
1.労働力不足
特に人口減少が進む地域では、設備保全に必要な技術者の確保が難しくなっています。この問題は、外国人労働者の採用や技術の自動化サービスを導入することで部分的に解決されつつあります。しかし、専門知識の取得とそれに関連するスキルの継続的な開発が依然として必要です。
2.多様な生産ニーズ
消費者のニーズが多様化する中で、工場は多品種少量生産に対応する必要があります。これにより、生産設備も複雑化し、保全作業が困難になっています。こうした多様なニーズに対応するためには、設備保全において柔軟かつ効率的なサービスが求められます。
3.短期の短縮要求
競争が激化する中で、より短い納期が求められるようになり、生産設備の稼働率が上昇します。これにより、設備の負荷が増し、保全の重要性がさらに高まります。
4.既存設備の老朽化
古い設備は故障しやすくなり、保全作業が増加します。また、新しい技術を導入するための更新費用も大きな課題です。
これらの課題に対応する解決策として、多くの業界では事後保全や予防保全から、より進んだ予知保全・予兆保全へとシフトする動きが見られます。予知保全・予兆保全は、設備の状態をより詳細に監視し、問題が発生する前に対処することを可能にし、生産効率の向上を実現します。これにより、保全作業の一覧管理が容易になり、より効果的なサービスが提供されるようになります。
設備保全の種類
この項目では保全方式の主な3つの種類として「予防保全」「事後保全」「予知保全」について解説します。
1.予防保全(Preventive Maintenance)
予防保全とは、機械・設備の機能の以上や不具合が発生する可能性がある場合に、予防的に行われる保全対策のことです。予防保全は、設備が安定して稼働し続けられるように、定期的にメンテナンスを行うことで、故障のリスクを減らし、設備の寿命を延ばし、全体的な運用コストを下げることを目指します。
具体的には、設備の耐用年数や使用時間を事前に設定し、これに基づいてメンテナンスや部品の交換を計画的に行います。これにより、故障が発生した場合の修理時間を短縮し、設備の稼働期間を最大化し、ライフサイクルコストの削減を図ることができます。
一方で、設備の状態を問わず、保全計画どおりに作業が実行されるため過度の保全、もしくは想定以上に早く劣化しているなどの不十分な状況が発生する可能性があります。
予防保全には「時間基準保全」と「状態基準保全」があります。
「時間基準保全」(TBM:Time Based Maintenance)
一定の期間や時間稼働した機械や設備を予防的に更新するという保全方式です。
時間基準保全には定期保全と経時保全があります。
通常、保守の間隔は、摩擦、老朽化、腐食などの要因を踏まえ、同じ種類の機械の過去の実績を基に設定されます。
保守の間隔を安全を最優先に短めに設定すると、部品がまだ使用可能な状態であるにも関わらず交換したり、問題がないにもかかわらず分解してメンテナンスを行うリスクがあります。しかし、コスト削減を重視し間隔を長く設定すると、突発的な故障が発生し製造ラインが停止するリスクや、大きな損失を招く可能性があります。
適切なメンテナンス間隔を設定しない場合、逆に損失や事故を引き起こす恐れがあるため、時間基準の保守管理を行う際は、慎重に間隔を決めることが求められます。
「状態基準保全」(CBM:Condition Based Maintenance)
生産機械や設備、部品の実際の状態や稼働状況を監視し、それらの劣化具合に合わせて定期的なメンテナンスを施す方法です。この手法により、設備が故障する前に適時に対処することで、余分なメンテナンス費用を削減できます。
しかしながら、設備の状態を正確に把握するためには高度な技術やシステムが必要とされ、これが個人の技量に依存することで、見落としのリスクになるというデメリットも伴います。設備の早期の劣化兆候を捉えることができれば、より進んだ「予知保全」を実現し、設備の保全において最適な対応が可能になります。
予防保全のメリット
・故障リスクの軽減
設備の定期的な点検やメンテナンスにより、故障のリスクを大幅に減少させることができる。これにより、設備の停止時間を最小限に抑えることができる。
・寿命の延長
適切なメンテナンスにより、設備の寿命を延ばすことができる。設備が長期間にわたって正常に稼働することで、新規設備投資の頻度を減らすことができる。
・コストの削減
予防保全を行うことで、突発的な故障による修理費用や生産ロスを減少させ、全体的な運用コストを削減することができる。
予防保全のデメリット
・過剰なメンテナンス
設備の実際の状態に即していない場合、必要以上のメンテナンスを行うリスクがある。これにより、無駄なコストが発生することがある。
・適切な閾値設定の難しさ
保全計画において適切なメンテナンス間隔を設定することは難しい。不適切な設定により、過剰なメンテナンスや必要なメンテナンスの見逃しが発生する可能性がある。
2.事後保全(Corrective Maintenance)
機械・設備の機能異常や不具合が発生した場合、故障し、生産ラインが停止した際に行うメンテナンスです。予防保全が行われていない場合や、予防保全を行っていても故障が発生した場合に実施されます。事後保全には「緊急保全」と「計画事後保全」があります。
「緊急保全」(Emergency Maintenance)
緊急保全とは、突発的におこった故障や生産設備の停止に対し、現場で直ちに修理などの保全作業を行う方法です。
「計画事後保全」(Planned Corrective Maintenance)
計画事後保全とは、あらかじめ代替え機械・設備を用意しておき、有事の際に切り替えることで設備機能が完全停止しないようにする方法です。予防保全が十分に行われていない場合や、故障が避けられない場合に適用されます。
事後保全のメリット
事後保全のメリットは、故障がおきなければ日々のメンテナンス費用が発生しないこと。故障しても部品の交換が短時間でできることがわかっており、 生産ラインへの影響も軽微な場合は、事後に対応することにメリットがある。
事後保全のデメリット
事後保全のデメリットは、部品や予備機などの設備を用意する必要があること。事後対応となるため、原因の調査に時間がかかる場合や、代替え機の手配状況により復旧までの時間がかかってしまう場合もある。
2.予知保全(Predictive Maintenance)
予知保全とは、機器の不具合の前兆を検出し対応することにより、メンテナンスのタイミングや頻度に関する無駄を減らすことができる保全手法です。IoTセンサーやAI技術を活用して設備の状態を監視し、異常が発生する前に対策を講じます。この方法は、トラブルの発生する可能性がある時点を事前に特定し、対策を講じることに重点を置いています。
「予兆保全」(Prognostic Maintenance)
IoTやAIの分析技術を活用して予兆を検出する予知保全は、予兆保全と称されることがあります。IoTやAIは、定期的なメンテナンスの回数を減らしつつ、トラブルが実際に発生する前に対処することが可能になるため、大きな期待が寄せられています。予知保全の一種で、設備の異常兆候をリアルタイムで監視し、異常が発生する前に迅速に対応する方法です。これにより、故障の発生を未然に防ぎ、生産効率を向上させることができます。
予知保全のメリット
・効率的なメンテナンス: 故障の兆候を事前に検出することで、計画的にメンテナンスを行い、無駄なメンテナンスを減らすことができる。
・ダウンタイムの最小化: 故障の発生を未然に防ぐことで、設備のダウンタイムを最小限に抑えることができる。
予知保全のデメリット
・初期コストの高さ: IoTセンサーやAI技術の導入には初期コストがかかるため、中小企業にとっては負担が大きい場合がある。
まとめ
食品工場で高品質な製品を安定して生産するためには、設備保全が不可欠です。設備保全の目的は、設備の機能維持、寿命延長、ライフサイクルコスト削減です。課題として労働力不足や多様な生産ニーズ、短納期要求、既存設備の老朽化が挙げられます。これらに対応するため、事後保全から予知保全へとシフトが進んでおり、IoTやAIを活用した効率的なメンテナンスが重要視されています。
FOOD TOWNでは他にも様々な食品業界に特化した内容を随時更新中です!
まずは下記から無料会員登録をお願いします!
お問合せはこちらまで
Robots Town株式会社
〒533-0033
大阪府大阪市東淀川区東中島1丁目17-5 941号室
TEL:06-4703-3098
関連リンク・資料