news
食品工場の安全対策とは?5S・ヒヤリハット・KYTを解説コラム
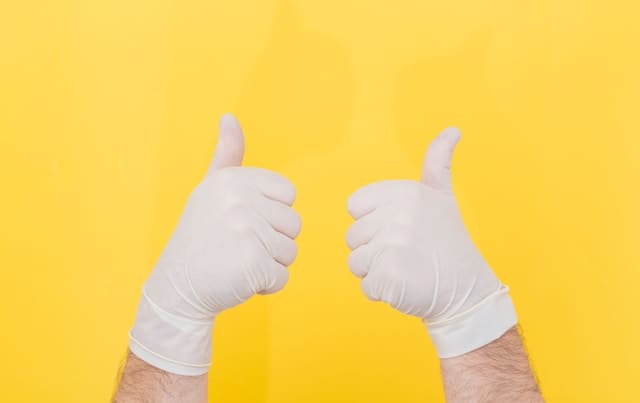
食品工場において、安全対策は生産性と品質の向上に直結する重要な要素です。特に、従業員の安全を確保するためには、作業環境の整備や危険を予防するための取り組みが欠かせません。本記事では、食品工場での安全対策として広く導入されている「5S」「ヒヤリハット」「KYT(危険予知トレーニング)」について詳しく解説します。
食品工場の安全対策がなぜ必要なのか?
食品などの工場の現場には多くの機械が動いており、重い資材、化学物質、高温など、さまざまな危険が伴います。安全管理が不十分な場合、死亡に至る事故が起こることもあります。
厚生労働省の報告によれば、2022年度に発生した労働災害による死亡者は、産業全体で774
人に上り、製造業では140人が死亡しています。産業全体での死傷者数は132,355人と過去20年で最多となりました。製造業では26,694人の死傷者数となり、原因として機械等による「はさまれ・巻き込まれ」と「墜落・転落」が多くを占めています。
事故が発生し、従業員が死傷する場合、企業は人的資源の損失に直面するだけでなく、損害賠償の請求を受けるリスクもあります。安全不備が原因で法律違反が認められると、罰金や刑事罰が課せられることもあります。
不適切な安全管理によるネガティブなイメージは、社会的信頼の失墜、人材獲得の難航、取引先からの信頼喪失による売上減少につながりかねません。
そのため、事業の継続性を保つためにも、適切な安全対策を講じることが極めて重要です。
食品工場の安全対策とは?
食品などの工場の現場で実施するべき主な安全対策について解説します。
5S活動を徹底する
5Sの具体的な実施方法
5Sを効果的に実施するためには、以下のステップが基本となります。
整理(Seiri): 必要なものと不要なものを分類し、不要なものを現場から排除します。これにより、無駄なスペースの確保や作業効率の低下を防ぎます。
整頓(Seiton): 必要なものを使いやすい場所に配置し、すぐに取り出せる状態を維持します。これにより、探す時間を短縮し、作業効率が向上します。
清掃(Seiso): 日常的に作業場を清掃し、汚れや異物の混入を防ぎます。これにより、清潔な環境が維持され、製品の品質が保証されます。
清潔(Seiketsu): 整理・整頓・清掃を徹底し、清潔な状態を維持します。定期的な点検や清掃スケジュールの策定が必要です。
しつけ(Shitsuke): 5Sを習慣化し、全従業員が日常業務で実践できるよう教育・訓練を行います。これにより、全社的な安全文化が根付くことを目指します。
5Sの成功は、継続的な改善と全従業員の協力が鍵となります。これにより、食品工場は安全で効率的な作業環境を維持し、品質の高い製品を提供することが可能となります。
これらの概念は英語でもSort(整理)、Set in order(整頓)、Shine(清掃)、Standardize(清潔)、Sustain(しつけ)として、頭文字が「S」になるように翻訳され、日本国内だけでなく全世界で広く採用されています。この5Sの原則に基づく取り組みを「5S活動」と称します。
5Sの効果
5Sの実施により、職場の安全性向上と業務効率化が期待されます。整理された職場では転倒事故のリスクが減少し、整頓された環境では潜在的な危険性を容易に識別できます。さらに、清掃と清潔を保つことは、転倒や転落のリスクを減らす上で不可欠です。
労働災害のリスクや予防策の重要性を理解し、身につける「しつけ」を通じて、工場の安全管理が強化されます。
また、整理整頓された清潔な職場は、必要な道具を迅速に見つけ出すことを可能にし、その結果、時間の浪費を減らします。快適な労働環境は従業員の働きやすさを促進し、結果として業務の生産性を高めることができます。
5Sのポイント
5S活動を成功させるためには「活動目的の明確化」が重要です。目標がはっきりしていないと、従業員の理解や協力を得るのが難しく、活動が曖昧なものになりがちです。従業員が5S活動を単なる上からの指示と感じている場合、その効果は限定的になります。従業員からのフィードバックを積極的に求めたり、規則作りに従業員を巻き込むなど、参加と貢献を促す工夫が求められます。
ヒヤリハットとは?その重要性と実践方法
ヒヤリハットとは、「ヒヤリ」とする瞬間と「ハッ」と気づく体験を組み合わせた言葉で、危うく大きな事故に繋がりそうな状況を指します。ヒヤリハットの目的は、大きな事故に繋がりそうな状況を特定し、予防策を講じることにあります。
ヒヤリハットは、精神的な不注意や焦り、情報の不共有、5Sが不十分な場合に発生しやすいと考えられています。
1.報告
従業員がヒヤリとした瞬間やハッとした出来事を即座に報告します。報告は紙ベースでもデジタルツールでも良いですが、迅速に行える仕組みを構築することが大切です。
2.分析
報告された事例を詳細に分析し、根本原因を探ります。この段階では、個々の事例を深掘りし、どのような要因が危険を引き起こしたのかを明確にします。
3.対策
分析結果に基づいて、具体的な改善策を策定し、実行します。改善策は全従業員に周知し、再発防止に努めます。
4.フォローアップ
実施された対策の効果を検証し、必要に応じてさらなる改善を行います。定期的な見直しと改良が重要です。
ヒヤリハットの効果
ヒヤリハット活動の実施により、大きな災害の発生を未然に防ぐことができると期待されています。
労働災害における経験則の「ハインリッヒの法則」では、ある人が引き起こす330の事故のうち、1件が重大な災害、29件が軽度の怪我、そして300件が無傷の出来事であるとされています。これは、多数のヒヤリハット事件が積み重なることで、最終的には1件の大きな事故につながる可能性があることを示しています。そのため、ヒヤリハット活動を通じてこれらの小さな事故を把握し、対策を講じることで、重大な事故の発生を防ぐことが可能になるわけです。
ヒヤリハットのポイント
ヒヤリハット活動を効果的に行うためには、「報告書の作成」、「原因の分析」、「対策の共有」がポイントとなります。
「報告書の作成」は、ヒヤリハット発生直後に行うことが重要です。時間が経過すると細かな詳細が忘れ去られがちなため、事象を新鮮な記憶のうちに文書化することが望ましいです。
「原因の分析」は、事象の背後にある原因を深掘りし、それを明らかにすることで、同様のヒヤリハットを未然に防ぐことが可能になります。
「対策の共有」では、実際の作業者の意見を取り入れた対策を策定し、それを広く周知することが重要です。例えば、掲示板への掲載を通じて、全員が対策を知り、理解することが必要です。
KYT(危険予知トレーニング)とは?その効果と実践方法
KYTの意義と目的
KYT(危険予知トレーニング)は、作業開始前に潜在的な危険を予測し、その対策を立てるための訓練です。食品工場では、新しい作業や機械を導入する際に、KYTを実施することで、作業に伴うリスクを事前に把握し、安全対策を講じることができます。
KYTの実施プロセス
KYTは、以下のプロセスを通じて行われます。
現場確認: 作業現場を確認し、どのようなリスクが潜在しているかを考えます。例えば、機械の配置や作業動線に問題がないかをチェックします。
リスク抽出: 潜在的な危険をリストアップし、優先順位をつけて対策を検討します。リスクは具体的に言語化し、誰もが理解できるようにすることが重要です。
対策立案: 抽出されたリスクに対する具体的な対策を策定します。この際、従業員の意見を取り入れ、現場に即した実用的な対策を立てることが求められます。
実施と評価: 対策を実施し、その効果を評価します。効果が不十分であれば、追加の対策を講じ、リスクを完全に取り除くように努めます。
KYT(危険予知トレーニング)の効果
KYT(危険予知トレーニング)を適用することで、ヒューマンエラーなどの心理的な状態を理解できるようになります。これにより、安全問題を個人の責任として捉える視点が養われ、リスクを予測するスキルが向上します。結果として、日々の業務や振る舞いにおいても注意が増し、労働災害の減少に結びつきます。
また、KYTは安全性の向上だけでなく、チームの結束力強化、リーダーシップ能力の育成、良質な職場文化の形成といった効果もあります。これによって、安全に関する議論や互いの支援が容易になり、安全対策の効果が高まります。
KYT(危険予知トレーニング)のポイント
KYT実施時には、各ラウンドにおけるポイントが存在します。
1Rの「現状把握」段階では、過去の出来事に囚われず、現在発生可能な危険をリストアップすることが 重要です。
2Rの「本質追求」では、単なる多数決に頼るのではなく、チームメンバーそれぞれの視点を統合することが要求されます。合意に達するまでの積極的なディスカッションが推奨されます。
3Rの「対策立案」では、日常の作業に適用が可能な実行計画の策定を目指します。
4Rの「目標設定」では、設定した目標を公開し、チーム全員がそれに沿って行動することが重要です。
まとめ
食品工場における安全対策は、5S、ヒヤリハット、KYTといった手法を組み合わせることで、より効果的に実施できます。これらの手法は、単独で行うだけでなく、相互に補完し合うことで、その効果を最大限に引き出すことが可能です。
例えば、5Sで整備されたクリーンで効率的な作業環境は、ヒヤリハットの報告やKYTの訓練がスムーズに行われる基盤となります。また、ヒヤリハットやKYTによって得られた知見は、5Sの取り組みをさらに強化するための貴重なフィードバックとなります。
安全文化の醸成
最後に、これらの手法を定着させるためには、全従業員が安全に対する意識を高め、日々の業務の中で自然に実践できる環境を整えることが不可欠です。企業として、安全を最優先に考え、継続的な教育と改善を進めることで、食品工場全体の安全性と生産性を飛躍的に向上させることができます。
このブログ記事が、食品工場での安全対策に取り組む多くの経営者や従業員にとって有益であることを願っています。また、これらの手法を活用し、さらに安全な職場環境を築き上げるための一助となれば幸いです。
FOOD TOWNでは他にも様々な食品業界に特化した内容を随時更新中です!
まずは下記から無料会員登録をお願いします!
お問合せはこちらまで
Robots Town株式会社
〒533-0033
大阪府大阪市東淀川区東中島1丁目17-5 941号室
TEL:06-4703-3098
関連リンク・資料