news
パレットチェンジャーの導入による生産性向上とリスク回避製品情報
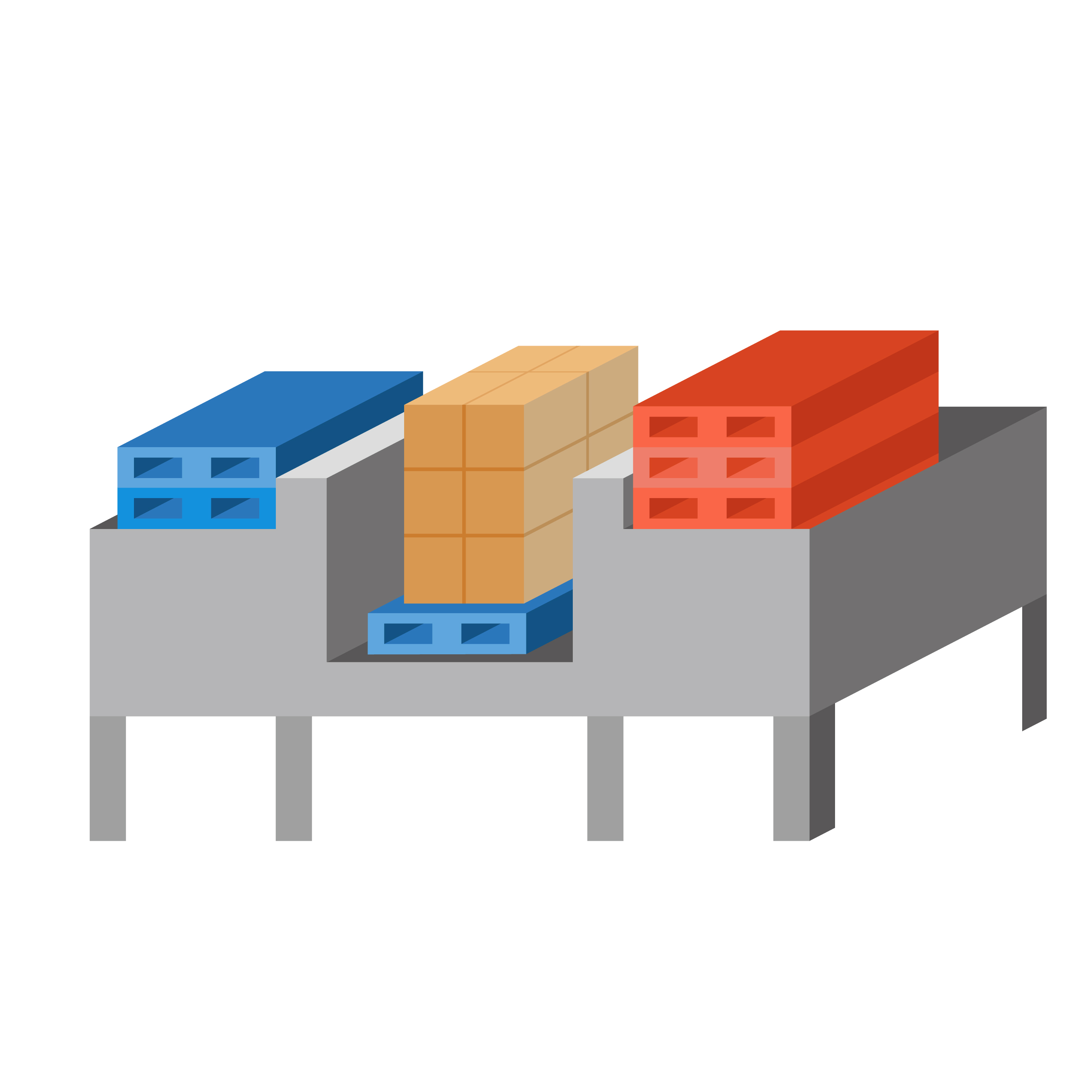
パレットチェンジャーの導入による生産性向上とリスク回避 – 食品工場における設備紹介
食品工場では、衛生管理と効率的な運用が重要視されています。 特に、混入リスクや作業効率の低下を防ぐために、新しい設備を導入することが求められています。この装置は、工場内外で使用されるパレットを効率的に考えることで、混入のリスクを軽減し、作業効率を大幅に向上させることができます。本記事では、パレットチェンジャーの基本情報や導入ポイントなどを詳しく解説します。
FOOD TOWNの【食品機械について学ぶ】では導入時のトラブル事例、種類、原理、使用用途、参考価格まで詳しく解説しています。
作業環境とパレットチェンジャーの適応性
特に食品工場では、衛生面が重視されるため、パレットチェンジャー自体が衛生基準に適合しているかを確認します。
作業環境の考慮
清掃の容易さ: 食品工場では定期的に清掃が行われるため、パレットチェンジャーの清掃がしやすいかどうか、装置の材質が衛生的であることが求められます。
耐久性と予防・防湿機能:パレットチェンジャーが湿気や粉塵が多い環境でも稼働できるか、また、予防・防湿機能があるか確認します。
対策
衛生管理対応のデバイス選定:清掃がしやすく、腐食や耐久に強い素材(ステンレスや特殊コーティング)を使用した装置を選定することで、長期的な衛生管理を簡単に行います。
保守とメンテナンス計画の考え方
パレットチェンジャーのような生産設備を長期的かつ効率的に運用するためには、保守とメンテナンス計画が非常に重要です。メンテナンス計画を正しく立てるために、設備の突然の故障や生産ラインの停止をここでは、保守と保守計画の考え方について解説します。
定期メンテナンスの重要性
定期的なメンテナンスは、設備の維持稼働率をし、予期せぬ故障を防ぐための準備です。機器が劣化する前に部品の交換や調整を行うことで、重大なトラブルの発生を防ぐことができます。
定期メンテナンスの内容
潤滑:可動部分の潤滑が不足すると、摩耗や異発生し、故障につながります。 定期的に適切な潤滑剤を使用して保守を行うことが重要です。
ボルトやナットの緩み確認:長時間の稼働によって、機器の固定部品が緩むことがあります。これを放置すると振動や異常動作が発生する可能性があるため、定期的に締め付け状態を確認します。
センサーのチェック:パレットチェンジャーに搭載されたセンサー(製品の位置やパレットの位置を検出するなど)の動作確認を行い、正常に作動しているか確認します。
メンテナンススケジュールの設定
機器の使用頻度や環境に配慮し、定期的なメンテナンススケジュールを立てます。一般的には、1ヶ月、3ヶ月、6ヶ月ごとの点検項目をリスト化し、計画的に実施します。
予防保全と災害保全の考え方
予防保全
予防は、設備が故障する前に事前にメンテナンスを行うことで、トラブルの発生を未然に防ぐ方法です。 定期的なメンテナンスや部品交換を計画的に行うことで、設備の寿命を兼ねて、突発ような生産停止を回避します。
部品の予防的交換:摩耗や劣化が予測される部品(ベルト、ギア、クランプなど)は、定期的に交換します。特に消耗品に該当する部品は、故障前に交換することで万が一の際、安定した運用が可能です。
点検記録の一時:各メンテナンス時の点検結果や部品交換の履歴を記録しておいて、設備の状態を把握し、次回のメンテナンス時期や部品交換のタイミングを正しく判断できます。
故障保全
故障保全は、設備が故障した際に対応する方法です。予防保全でカバーできない予期せぬ故障が発生した際、迅速に修理対応できる体制を整えておくことが重要です。
緊急対応手順の準備:故障が発生した際の対応手順を明確にし、迅速に修理が決まるようにしておきます。 特に、緊急時にはどの部分を確認すべきか、どの作業者が対応すべきか明確にし取っておくことが重要です。
対策
故障やメンテナンスの際に必要な部品を事前準備しておりますので、故障時のダウンタイムを極力抑えられます。 特にが予想される部品については、十分な在庫を確保しますしておくことが必要です。
パレットチェンジャーの洗浄と衛生管理
食品工場では、衛生管理も重要なこととなります。パレットチェンジャーが清潔に保たれてメンテナンスされていないと、騒音混入や食品の品質低下を図る可能性があります。そのため、定期的なクリーニングが必須です。
クリーニングの要点
可動部分の清掃
パレットチェンジャーのクランプやスライド部分に汚れやクオリティがたまると、動作が不安定になり、故障の原因となります。
防錆対策
設備の金属部分は、錆びないように適切な防錆処理を別途必要があります。特に湿度の高い場所で使用される場合は、定期的に防錆剤を使用してメンテナンスを行いますます。
食品安全基準の遵守
使用する清掃剤やメンテナンス用品は、食品安全基準に適合していることが重要です。安全な洗浄方法を徹底し、食品工場の衛生基準に合った洗浄を行います。
長期的なメンテナンス計画の策定
長期メンテナンスのポイント
設備のライフサイクル管理
設備の導入から廃棄までのライフサイクルを考慮し、各段階でのメンテナンス計画を立てます。
データに基づく改善
メンテナンスの結果をデータとして残し、次回以降の改善に保留します。たとえば、特定の部品がどれくらいの頻度で劣化するかのデータをとり、交換タイミングを最適化します。
保守計画の定期的な見直し
長期的な計画は、設備の使用状況や工場の運用状況に応じて保守して、定期的に見直しを行います。これにより、最新の情報に基づいた最適な保守が可能になります。
パレットチェンジャーの導入事例
食品工場におけるパレットチェンジャーの導入事例を紹介します。
大手食品メーカーでの導入事例
工場内の製造ラインと出荷作業を効率化するためにパレットチェンジャーを導入しました。この工場では、屋外で使用するパレットと工場内専用のパレットが使われており、従来は手動でパレットの積み替え作業を行っていました。しかし、手動作業には多くの時間がかかり、作業負担が大きいため課題でした。
導入の目的
作業効率の向上: 手動でのパレット交換作業が非効率であり、時間がかかっていたため、パレットチェンジャーを導入することで、作業時間の短縮を図りました。
労働災害のリスク軽減: 重い製品を手作業で持ち上げることが、作業員の負担となり、腰痛などの労働災害のリスクを覚悟してきました。 パレットチェンジャーによって作業の自動化を進めることで、これらのリスクを低減することを目的としました。
結果
作業時間の大幅短縮: パレットチェンを導入することで、パレットジャーの残り作業時間が従来の半分に短縮されました。これにより、出荷作業全体の効率が向上し、作業の流れがスムーズになりました。
作業負担の軽減: 重い製品の引き上げ作業がなくなり、作業員の体への負担が大幅に軽減されました。これにより、作業員の安全性も向上し、労働災害のリスクが低下しました。
中小食品工場での混入対策
工場内と外部で使用するパレットを明確に区別して使用していましたが、手動でのパレット交換に伴い、混入のリスクが発生していました。戻ってきたパレットを再び工場内に持ち込む際、パレットに蓄積したゴミを工場内に持ち込む危険性があったのです。
導入の目的
異物混入リスクの低減: 工場内外でのパレットの使用を区別する際に、パレットチェンジャーを活用して外部用パレットを工場内に持ち込まず、異物混入リスクを抑制することが目的でした。
作業の標準化:手作業でのパレット交換に伴う作業のばらつきがあり、作業ミスが発生することがあったため、自動化による作業の標準化も課題となっていました。
結果
異物混入の防止: パレットチェンジャーを導入することで、工場外からの異物混入リスクが大幅に減少しました。 特に衛生管理が厳しい工場では、衛生基準を維持するために大きな効果を発揮しました。
作業の均一化: 自動化されたパレットチェンジャーによって、作業が標準化され、作業ミスの発生がほぼなくなりました。これにより、工場全体の生産品質も向上しました。
原材料倉庫での労働効率改善
原材料を順番倉庫では、外部から搬入された原材料を工場内専用パレットに積み替える作業が頻繁に発生していました。手作業でのパレット交換は作業員の負担が大きく、特に重量物の扱いに時間がかかっていたため、作業効率が課題となっていました。
導入の目的
作業の自動化による負担軽減: 重量物をめぐる際の作業負担を軽減し、作業員の疲労やミスを軽減するためにパレットチェンジャーを導入しました。
倉庫内作業の効率化:パレットチェンジャーを導入することで、パレット交換作業の自動化を進め、倉庫内作業全体の効率を向上させることが目標でした。
結果
作業時間の短縮: パレットチェンジャーの導入により、原材料のパレット交換作業が自動化され、作業時間が大幅に短縮されました。作業効率が向上したことで、倉庫内の他の業務にも時間を割くことができますができるようになりました。
労働負担の軽減: 重量を手作業で行う機会が減少し、作業員の負担が軽減されました。これにより、作業の安全性も向上し、疲労やケガのリスクが軽減されました。
まとめ
パレットチェンジャーの導入は、食品工場における生産性の向上やリスク回避に非常に効果的です。食品工場では、衛生管理や効率的な運用が重要視されており、パレットチェンジャーの導入によりリスク混入や作業負担の軽減、作業の安全性の向上が期待できます。
導入事例では、大手食品メーカーや中小規模の工場でパレットチェンジャーが導入され、作業時間の大幅短縮や大量混入リスクの防止、作業の自動化による負担軽減といった具体的な成果が報告されています。また、パレットチェンジャーは食品工場に関して重要な設備であることがわかります。
今後、さらに多くの食品工場がパレットチェンジャーを導入することで、より効率的で安全な生産環境を構築していくことが期待されます。
FOOD TOWNでは他にも様々な食品業界に特化した内容を随時更新中です!
まずは下記から無料会員登録をお願いします!
今後もFOOD TOWNをよろしくお願いいたします。
お問い合わせは下記までお願いいたします。
FOODTOWN担当
E-mail:info@food-town.jp
TEL:06-4703-3098
FOOD TOWNサイトURL:https://food-town.jp/
関連リンク・資料