news
食品工場の異物混入を防げ!調査の手順と再発防止策を分かりやすく解説コラム
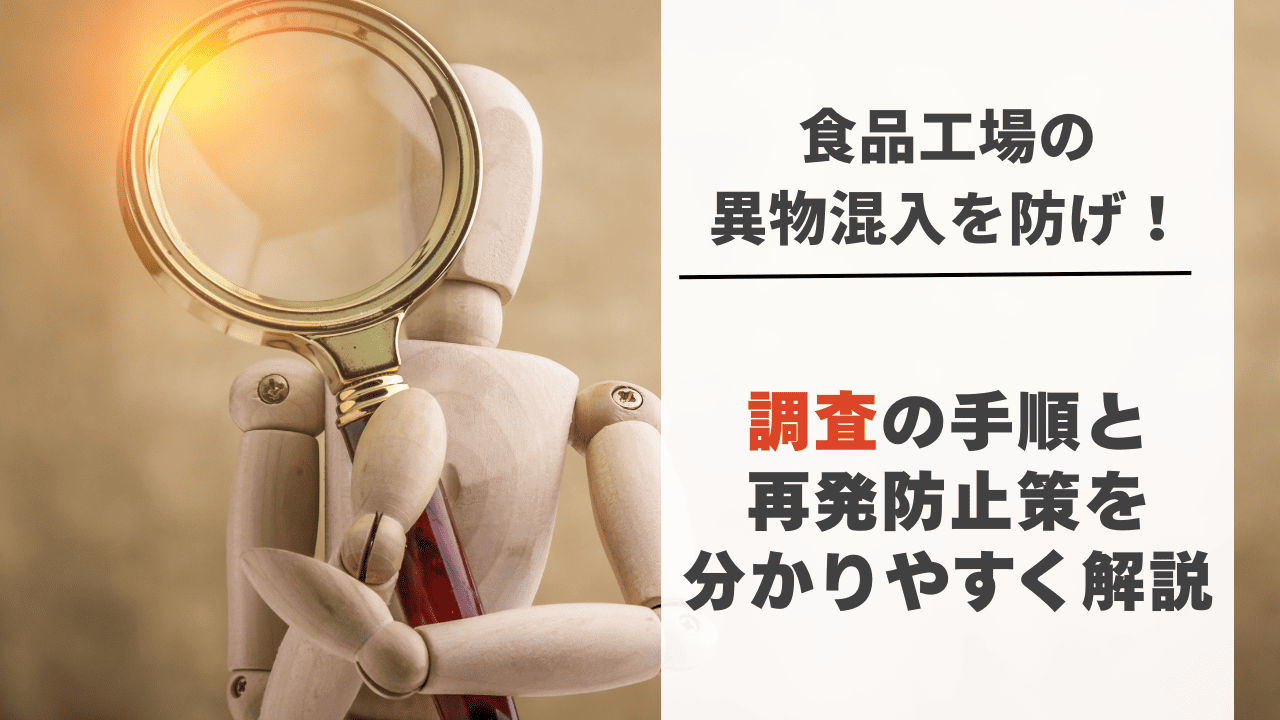
異物混入が起これば、製品回収・信用失墜・取引停止など甚大な損失につながります。最も重要なのは「再発を防ぐこと」。その第一歩が、外部機関に依頼する前に社内で迅速かつ的確に原因を掴むことです。本記事では、現場担当者でも実践できる社内調査のステップを網羅し、再発防止に直結する実例とツールを紹介します。
社内調査が求められる3つの理由
異物混入が発生した際、すぐに外部機関に依頼するのではなく、まずは自社内で初期調査を行うことが重要です。社内対応には、スピード感、コスト意識、そして知見の蓄積といった複数のメリットがあります。ここでは、なぜ今「社内調査」が求められているのか、3つの観点からその理由を解説します。
スピード感
外部依頼の平均リードタイムは数日〜1週間程度とされており、混入の内容や分析対象によってはさらに日数がかかることもあります。特に緊急対応が求められる食品工場では、調査を社内で迅速に実施できる体制があるだけで、対策の着手までの時間を大幅に短縮することが可能です。この初動スピードの差が、製品の出荷可否判断やクレーム対応のタイミングにも直結します。
コスト意識
成分分析1件あたりの料金の相場はおおよそ5万〜10万円程度とされており、分析内容や検査項目によってはさらに高額になることもあります。そのため、社内である程度まで原因を絞り込み、不要な検査を省くことができれば、必要最低限の外部検査で済ませることが可能となり、コストの大幅削減につながります。特に小規模事業者にとっては、この点が大きなメリットとなります。
知見の蓄積
調査プロセスと結果を記録・共有することで、工場全体の品質管理レベルが底上げされると同時に、過去のトラブルから学びを得る「組織的学習」の機会ともなります。さらに、各工程での異常やクレーム対応履歴を体系的に整理することで、次の改善活動に役立つナレッジベースの構築も進み、全社的な品質文化の向上にもつながります。
初動対応のゴールとNG行動
異物混入が発覚した場合、すぐに行うべき対応の流れを整理しておくことが重要です。特に社内で対応可能な範囲を明確にしておくことで、スムーズな実施と情報共有が可能になります。また、想定されるNG行動を事前に知っておくことで、再発や拡大リスクを抑えることができます。以下に、初動で行うべきことと避けるべき行為を分かりやすく解説します。
初動対応のゴール
1.混入経路の仮説を立てる
どこでどのように異物が混入したのか、製造プロセスや搬送経路、作業者の行動記録をもとに仮説を立てます。
2.関係部署と共有し、被害範囲を把握する
品質管理部門や製造、保全、物流などの関連部署と速やかに情報を共有し、被害範囲や在庫の状況を確認します。
3.製造ラインの稼働可否を判断する
被害が拡大するリスクを考慮し、原因未確定のままラインを動かすか一時停止するかを経営判断と連携して決定します。
初動対応のNG行為
NG行動を事前に把握しておくことで、対応ミスによる二次被害や証拠の消失を防ぐことができます。以下に、現場でありがちなNG行動とそのリスクをまとめました。
1.異物を素手で触る
二次汚染・証拠毀損のリスクがあります。
2.撮影前に異物を移動
位置情報が失われ、原因特定が困難となるリスクがあります。
3.調査記録を口頭のみで共有
情報が属人化し、検証不能となるリスクがあります。
社内で実践する「4つの管理視点」
調査・検査・分析は 「人」「記録」「環境」「比較」 の4視点で整理すると漏れがありません。定性的な観察から始め、種類別に評価する流れを構築することで、正確な報告書の作成にもつながります。
1. 人の管理 ―― 衛生と役割分担
- 調査チームを3名程度で編成(採取・撮影・記録を分担)
- 衛生規定に基づき、手袋・マスク・キャップを必須着用
- 調査手順書を掲示し、手順逸脱を防止
2. 記録の管理 ―― デジタルと紙のダブル保存
- 写真+動画で「発見時の状態」を時系列保存
- 製造ロット、オペレーター、機械稼働ログを電子フォーマットで入力
- 記録変更はバージョン管理を行い、タイムスタンプを自動付与
3. 環境の管理 ―― 再発防止の基礎情報
- 発見場所の照度・温度・湿度・清掃状況を即時記録
- 異臭や変色の有無も記録に含める
- 隣接ラインや倉庫も含め半径5m以内を重点点検
4. 比較と分析 ―― 5分でできる同定フロー
- 肉眼観察:色・形状・質感をチェック
- ルーペ/簡易顕微鏡:表面構造を観察
- 重量測定:1/100g単位で同質素材を絞り込む
- 社内サンプルライブラリと照合
- 一致しない場合のみDNA分析や外部機関への依頼へ
【実例3選】社内調査で原因を特定したケース
ここでは、実際に社内調査を通じて異物の発見・原因究明・再発防止に成功した事例を紹介します。各ケースでは、異物の特性に応じて調査方法や使用する機器を選定し、評価や推定を通じて原因を特定しました。
事例①:プラスチック片の混入
発見物
青色0.5cmの破片
調査方法
ルーペと照明を用いた外観確認のうえ、作業現場の備品を照合。破片の一部を実体顕微鏡で観察し、バインダー素材との表面構造一致を確認。
調査結果
ラインチェック用バインダーの割れと一致
対策
紙製ファイルへ変更+備品点検頻度を週1→毎日へ
事例②:毛髪の混入
発見物
黒髪20cm
調査方法
更衣室周辺の清掃記録や防塵状況を確認。動線マップを用いて発見エリアとの関連性を評価し、ロッカーの材質や配置にも着目。必要に応じて社内の衛生映像を確認。
調査結果
更衣室動線で発塵が多発。ロッカー高さ不足が原因
対策
ロッカーを男女別・作業区別で分離し、清掃強化
事例③:黒ゴム片の混入
発見物
3mm角の弾力ある片
調査方法
破片の断面をルーペで観察し、同様の搬送装置部品と材質を比較。表面に残る劣化パターン(ひび割れや摩耗)をチェックし、材質評価のために一部を分析。
調査結果
搬送装置ローラーのゴム劣化片と同定
対策
耐油ゴムへ素材変更+点検周期を半年→月次へ
まとめ・関連記事
すべては「再発防止」のために
社内調査を仕組み化すれば、初動48時間以内に原因を80%以上特定できるようになります。4つの管理視点と実例に基づいた改善策を積み上げることで、工場全体の品質管理成熟度は着実に高まり、再発リスクを抑える体制が整います。また、外部機関による調査は「深掘り分析」に特化させ、日常的な対応は社内で迅速に仮説検証できる文化を築くことが理想的です。
関連記事
FOOD TOWNでは他にも様々な食品業界に特化した内容を随時更新中です!
まずは下記から無料会員登録をお願いします!
お問合せはこちらまで
Robots Town株式会社
〒532-0011
大阪府大阪市淀川区西中島6丁目6-17 RIC1st.ビル 501号室
TEL:06-4703-3098