news
食品工場のコスト削減術|電気・空調・水道…ユーティリティコストを見直す5つのポイントコラム
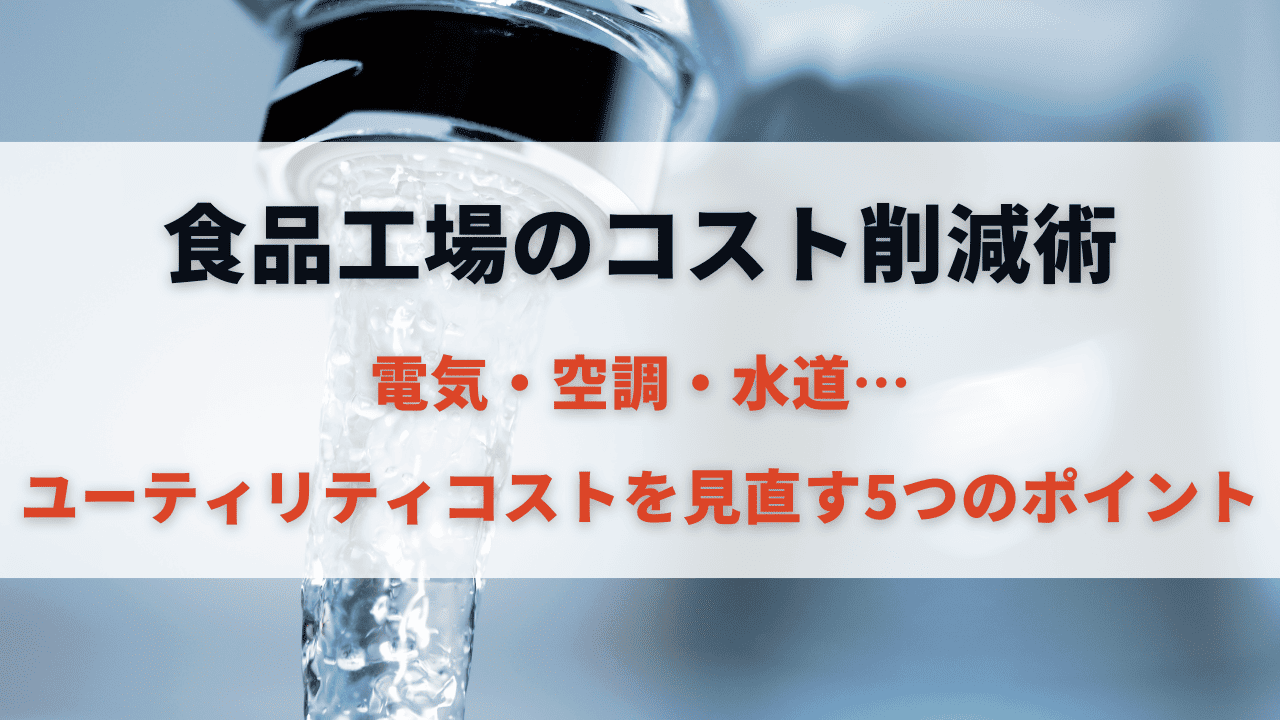
食品工場では、原材料費や人件費の上昇が注目されがちですが、実は見過ごされやすい「ユーティリティコスト(電気・空調・水道)」にも大きな削減余地があります。ユーティリティコストは一見すると固定費のように見えますが、運用の工夫や設備の更新によって大きく変動する“管理可能なコスト”でもあります。
本記事では、電気・空調・水道といったエネルギーコストを効率的に見直す5つの実践ポイントと、現場主導で成果を上げるための考え方を解説します。
電気・空調・水道は「見えづらい固定費」
食品工場のユーティリティコストの内訳とは?
ユーティリティコストとは、製造ラインを支える電気、空調、水道といったインフラにかかる費用のことです。食品工場では、冷蔵・冷凍設備や加熱機器、空調システムの稼働により、他業種に比べてもこれらのコスト比率が高くなりがちです。
実際のコスト比率は?
たとえば、冷凍食品や乳製品、調味料などを扱う工場では、全体の電気代のうち約40〜60%を冷却・冷凍設備が占めているという例もあります。また、洗浄工程が多い場合には水道代や排水処理費用が原材料費よりも高くなることもあります。
人件費よりも高い場合も!“隠れコスト”に注意
特に24時間稼働の工場や、夏場・冬場の空調負荷が大きい現場では、ユーティリティコストが人件費を上回るケースもあります。それにもかかわらず、「固定費だから削減できない」「管理できないコスト」と誤解されやすく、対策が後回しになる傾向があります。
設備だけでなく運用管理にも注目を
無意識のムダをチェック
老朽化した設備の更新はもちろん重要ですが、それ以上に日々の運用方法に無駄が潜んでいることも少なくありません。たとえば空調の使い方、水の出しっぱなし、夜間の機器未停止などです。運用改善と設備投資の両面から見直すことが、効果的な削減の第一歩となります。
ユーティリティコスト削減の5つの見直しポイント
1. 古い設備の高効率化(インバーター・LED化など)
省エネ機器に更新
高圧受電設備や照明、モーター類など、エネルギーを大量に消費する設備を省エネ型に更新することで、長期的なコスト削減が見込めます。特にインバーター制御の導入やLED照明への切り替えは、初期投資を抑えつつ早期に効果が表れやすい施策です。
補助金も活用しよう
食品業界では、防水仕様や耐熱性の要件が厳しいため、専用機器を選定する必要があります。補助金制度を活用しながら進めることで、費用対効果の高い更新が可能です。
2. 空調のゾーニングと適正温度管理
ゾーン分けがポイント
広い工場内すべてを一律で冷暖房するのではなく、作業エリアごとにゾーンを分け、適正な温度管理を行うことで無駄な空調エネルギーを抑えることができます。人の動きや時間帯に応じた制御も効果的です。
実例:10%削減の工場も
たとえば製品の品質維持に必要な低温エリアと、包装・出荷のエリアで空調設定を分けるだけでも、エネルギー消費を10%以上削減できた例もあります。
3. 排水・水使用量のチェックと再利用技術の検討
水の見える化を進める
食品工場では洗浄工程で大量の水を使用します。**用途別の使用量を「見える化」**し、再利用できる水を活用することで、水道料金の大幅削減が可能になります。
再利用でコスト減
すすぎ水の再利用、熱交換器による温水回収など、工場の規模に応じた再利用設備が増えています。これにより、月額数万円〜数十万円規模のコストカットが期待できます。
高圧受電設備や照明、モーター類など、エネルギーを大量に消費する設備を省エネ型に更新することで、長期的なコスト削減が見込めます。特にインバーター制御の導入やLED照明への切り替えは、初期投資を抑えつつ早期に効果が表れやすい施策です。
4. 電気契約プラン・ピーク電力の最適化
契約プランを見直す
契約電力の見直しやピークカット制御により、基本料金の削減が可能です。稼働状況に合わせた電力契約プランへの変更やピーク時間帯の使用量調整が有効です。
タイマー制御も有効
ピーク時間を避けた仕込みスケジュールへの調整や、大型機械の同時稼働を回避するタイマー制御など、小さな工夫の積み重ねが効果を発揮します。
5. 定期点検とセンサーによる見える化・自動制御
定期点検でトラブル防止
ユーティリティ設備の点検を定期的に行うことで、漏電や無駄な稼働を未然に防止できます。
IoT導入で自動化
センサーやIoT機器を活用して使用状況を「見える化」し、自動制御することで、省エネと品質維持の両立が可能になります。特に温度ロガーや警報センサーはトラブル防止にも有効です。
現場・保全部門・経営の連携がカギ
ユーティリティコストの削減には、現場だけでなく経営・保全部門との連携が不可欠です。全体で取り組むことで、改善の継続と実行が可能になります。
部分最適では成果が出ない理由
現場単独では、投資判断や予算化が遅れがちです。全社視点での取り組みが、削減のカギを握ります。
「使い方」こそ最大の改善余地
最新設備を入れても、使い方が非効率では効果が出ません。電源オフの徹底や水の無駄遣い防止など、小さな積み重ねが差を生みます。
エネルギー専門業者との協働も有効
外部支援を活用することで、補助金の申請や改善提案がスムーズになります。「省エネ診断」などの無料制度も利用しましょう。
まとめ|エネルギーを“管理できるコスト”に
電気・空調・水道といったユーティリティは、削減が難しいと思われがちですが、運用の見直しや設備の最適化により、管理可能なコストへと変えていくことができます。
まずは「現状を見える化」することが第一歩です。潤滑剤や包材・副資材とあわせて取り組むことで、工場全体のコスト構造改革につなげていきましょう。
関連記事はこちら:
FOOD TOWNでは他にも様々な食品業界に特化した内容を随時更新中です!
まずは下記から無料会員登録をお願いします!
お問合せはこちらまで
Robots Town株式会社
〒532-0011
大阪府大阪市淀川区西中島6丁目6-17 RIC1st.ビル 501号室
TEL:06-4703-3098