news
食品工場の歩留まりを劇的に改善!ポイントを解説コラム
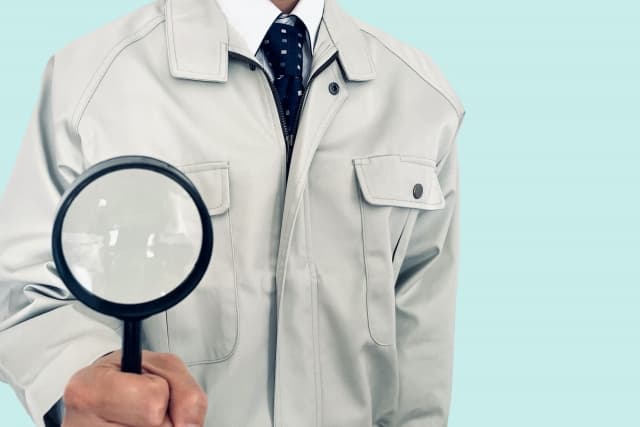
食品工場における歩留まりの改善は、生産効率を向上させるだけでなく、コスト削減や品質向上にも直結する重要な課題です。この記事では、歩留まり改善のための具体的な方法と、実際に成功した事例を紹介します。食品工場での歩留まり率を劇的に向上させるためのヒントを探している方は、ぜひ参考にしてください。
歩留まりの基本概念とその重要性
食品工場において歩留まりを向上させることは、原材料の無駄を減らし、生産効率を高めるための鍵です。しかし、歩留まり率=良品率ではありません。製造業においては違いを理解しておく必要があります。
歩留まり率とは?
歩留まり率とは、投入された原材料に対して、最終的に得られる製品の割合を示す指標です。歩留まり率が高いほど、原材料が効率的に製品に変換されていることを意味します。
・計算方法
歩留まり(%)=(得られた製品の重量/投入された原材料の重量)× 100
・例
100kgの原材料を投入し、最終的に80kgの製品が得られた場合、歩留まり率は80%です。
良品率とは?
良品率とは、製造工程で生産された製品の中で、基準を満たしている良品の割合を示す指標です。良品率が高いほど、品質が安定していることを意味します。
・計算方法
良品率(%)= 良品数÷完成品数×100
・例
100個の製品を生産し、そのうち90個が基準を満たしている場合、良品率は90%です。
具体例での比較
例を使って歩留まり率と良品率の違いをさらに具体的に理解しましょう。
例:パン工場
歩留まり率
原材料:小麦粉100kg
製品:パン80kg
歩留まり率 = 80÷100×100=80%
良品率
生産したパンの数:100個
良品の数:90個
良品率 = 90÷100×100=80%
このように、歩留まり率は原材料の使用効率を、良品率は製品の品質を評価するための指標としてそれぞれ異なる側面から工場のパフォーマンスを測定します。これらの指標を併用することで、より総合的な改善策を講じることが可能になります。
違いのまとめ
・対象
歩留まり率=原材料と最終製品の重量の割合
良品率=製品全体に対する良品の割合
・目的
歩留まり率=原材料の利用効率を評価
良品率=製品の品質を評価
・改善対象
歩留まり率=原材料の選定、加工プロセスの最適化、無駄の削減
良品率=製造工程の品質管理、検査プロセスの強化、従業員の訓練
歩留まり率の重要性
歩留まり率を高めることで、コスト削減(材料の無駄を減らすことで直接的なコスト削減が可能)、廃棄物削減(無駄を減らすことで、廃棄物の量を減らし、環境負荷を軽減)、製品の一貫性向上(安定した品質の製品を提供できるため、顧客満足度が向上)が期待できます。
歩留まり改善の具体的な方法
原材料の選定と管理
高品質の原材料の選定
原材料の質が最終製品の質に直結します。高品質な原材料を選定することで、歩留まり率が向上します。高品質な野菜や果物を選ぶことで、加工時のロスが減少し、歩留まり率が向上します。
サプライチェーンの最適化
信頼できるサプライヤーと連携し、安定した供給を確保することが重要です。サプライヤーとの契約を見直し、安定供給を確保することで、原材料の品質が一定になり、歩留まりが向上します。また、トレーサビリティの導入により原材料の入手元から製品に至るまでの流れを把握することで、品質管理が容易になります。
製造プロセスの最適化
標準作業手順の確立
標準化された作業手順を導入し、従業員が一貫した方法で作業を行えるようにします。作業手順書を作成し、全従業員にトレーニングを実施することで、作業ミスが減少します。また、作業手順を視覚的に示すことで、従業員が理解しやすく、ミスを防止できます。
自動化技術の導入
自動化された機械やロボットを導入することで、ヒューマンエラーを減少させ、歩留まり率を向上させます。パッケージング工程にロボットを導入し、製品の破損やミスを減少させることで、歩留まりが向上します。また、製造ラインにセンサーを設置し、リアルタイムでデータを収集・分析することで、問題を迅速に発見・解決できます。
品質管理の徹底
リアルタイムデータの活用
製造過程のデータをリアルタイムで監視し、問題が発生した際には即座に対処します。製造ラインにセンサーを設置し、データを収集・分析することで、異常が発生した場合に即座に対応できます。また、大量のデータを解析することで、潜在的な問題点を事前に発見し、予防措置を講じることもできます。
品質検査の強化
定期的な品質検査を行い、製品の不良率を低減させます。製品ごとにサンプルを取り、品質検査を行うことで、不良品の流出を防ぎます。自動化された検査システムを導入することにより、効率的かつ正確な品質検査を実現することができます。
歩留まり改善の成功事例
事例1 ABC食品工場
【背景】
ABC食品工場では、原材料の無駄が多く、歩留まり率が低いという課題に直面していました。
【改善策】
高品質な原材料の導入、自動化技術の採用、標準作業手順の確立を行いました。具体策としては、新しいサプライヤーと契約し、品質の高い原材料を安定的に供給。包装工程に自動化システムを導入し、標準作業手順を全従業員に教育しました。また、製造過程で発生するデータを分析し、ボトルネックを特定して改善しました。
【結果】
歩留まり率が20%向上し、年間コストが大幅に削減されました。年間で100万円以上のコスト削減に成功し、製品の一貫性も向上しました。
事例2 XYZ食品工場
【背景】
XYZ食品工場では、製品の不良率が高く、品質の一貫性に問題がありました。
【改善策】
リアルタイムデータの活用、品質検査の強化、従業員の教育訓練を実施しました。具体策としては、製造ラインにセンサーを設置し、データをリアルタイムで監視。定期的な品質検査と従業員トレーニングを実施しました。また、予防保全として、設備のメンテナンスを定期的に行い、故障を未然に防ぐように努めました。
【結果】
製品の不良率が30%減少し、顧客満足度が向上しました。不良品の流出が減り、クレームが50%減少。顧客からの評価も向上しました。
歩留まり改善のための実践的なヒント
従業員の教育訓練
従業員に対して定期的な教育訓練を実施し、製造プロセスに関する知識とスキルを向上させます。
【具体例】
月に一度の研修を実施し、新しい技術や作業手順を共有する。異なる部門の従業員が協力(クロスファクショナルチームの結成)し、歩留まり改善のアイデアを出し合う。
継続的な改善活動
PDCAサイクル(計画・実行・確認・改善)を導入し、継続的に改善活動を行います。
【具体例】
定期的に製造プロセスを見直し、改善点を特定し、実行する。従業員から改善提案を募り、小さな改善を積み重ねる(カイゼン活動)。
外部専門家の活用
必要に応じて、外部の専門家やコンサルタントの助言を受けることで、より効果的な改善策を導入できます。
【具体例】
生産効率改善のコンサルタントを招き、製造ラインの最適化を図る。他の工場と比較し、優れた事例を参考にする(業界ベンチマーク)。
まとめ
食品工場の歩留まりを劇的に改善するためには、原材料の選定から製造プロセスの最適化、品質管理の徹底まで、多岐にわたる取り組みが必要です。具体的な方法と成功事例を参考に、自社の工場でも歩留まり改善に取り組んでみてください。効率的な生産と高品質な製品を実現し、競争力を高めることができるでしょう。
関連記事
農業サプライチェーンとは?仕組みと課題、デジタル化による解決策を徹底解説
食品工場の役立つコスト削減アイデアやコスト削減の成功事例を解説
食品工場のコスト削減術|潤滑剤見直しで大幅コストダウンも可能?チェックリスト付き
FOOD TOWNでは他にも様々な食品業界に特化した内容を随時更新中です!
まずは下記から無料会員登録をお願いします!
お問合せはこちらまで
Robots Town株式会社
〒532-0011
大阪府大阪市淀川区西中島6丁目6-17 RIC1st.ビル 501号室
TEL:06-4703-3098
関連リンク・資料