FOODTOWNアドバイザーが
製品倉庫を徹底解説!
FOODTOWNアドバイザーが
製品倉庫を徹底解説!
製品倉庫とは?
製品倉庫ラックシステムは、生産途中の仕掛品や出荷前の完成製品を効率的に保管するためのシステムです。従来の方法では難しかった保管効率の向上を実現し、倉庫の床面積の約60%を保管に使用する高層ラックや立体ラックを活用して、在庫管理、入出庫、ピッキングの合理化など、ロジスティクス業務全般をカバーします。自動搬送ロボットや無人搬送車(AGV)、シャトルシステム、倉庫管理システムと連携することで、作業の自動化とヒューマンエラーの防止が可能となり、従業員の生産性も向上します。
このシステムは、物流センターや工場など複数の拠点で導入され、それぞれの施設の特性に合った最適なソリューションを提供します。効率的な空間利用、自動化技術、人材不足対応、正確な在庫管理が導入のポイントです。トレイ型のラックや高速シャトルシステムなども注目されており、入庫から仕分けまでのプロセスを最適化することで、供給の効率を高めます。24時間稼働可能なシステムにより、人件費の削減と高効率化が期待でき、物流課題の解決に大きな価値を提供します。
具体的な導入事例としては、工場での在庫管理の効率化や、物流センターでの自動搬送車を使った入庫から仕分けまでのプロセスの最適化が挙げられます。これにより、各施設での作業時間が短縮され、従業員の労働負担が軽減されます。また、統合されたシステムは、関連情報をリアルタイムで提供し、迅速な意思決定をサポートします。そのため、製品倉庫ラックシステムは、企業の生産性向上とコスト削減に大いに役立ちます。
導入には既存システムとの連携や専門的な知識が必要ですが、システムの価値を理解し、簡単に運用できるようにすることで、多くの企業にとって重要なソリューションとなるでしょう。物流システム全体の効率化を図るための提案や導入事例を基に、気軽に相談し、次のステップへの具体的な計画を立てることが重要です。これにより、台車や機器を運びやすくし、各プロセスがスムーズにつながり、全体の業務効率が上がることで、企業の競争力を高めることが期待されます。
以下では、製品倉庫ラックシステムの種類、導入ポイント、おおよその価格について詳しく解説します。
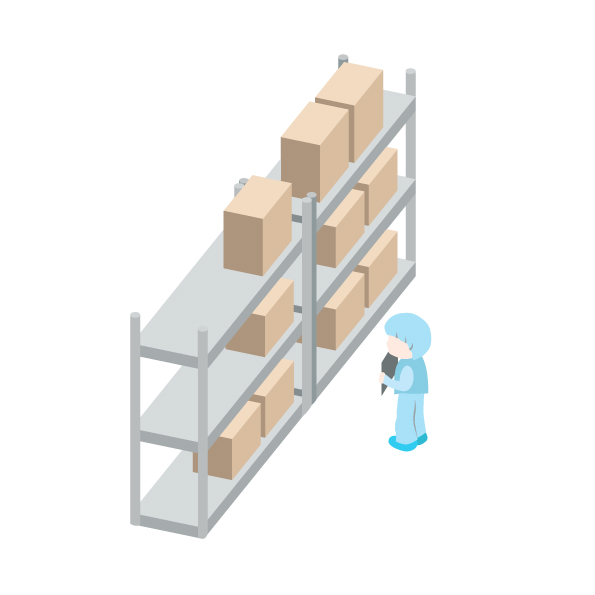
-
製品倉庫ラックシステムの種類、原理、使用用途について
-
製品倉庫ラックシステム価格について
-
製品倉庫ラックシステムの選定ポイント、導入時の確認ポイントについて
-
製品倉庫ラックシステム導入後のトラブル事例と事前対策ポイントについて
製品詳細確認・カタログ無料ダウンロード可能
「いろんな製品があって選ぶ基準が分からない…」そんなアナタに
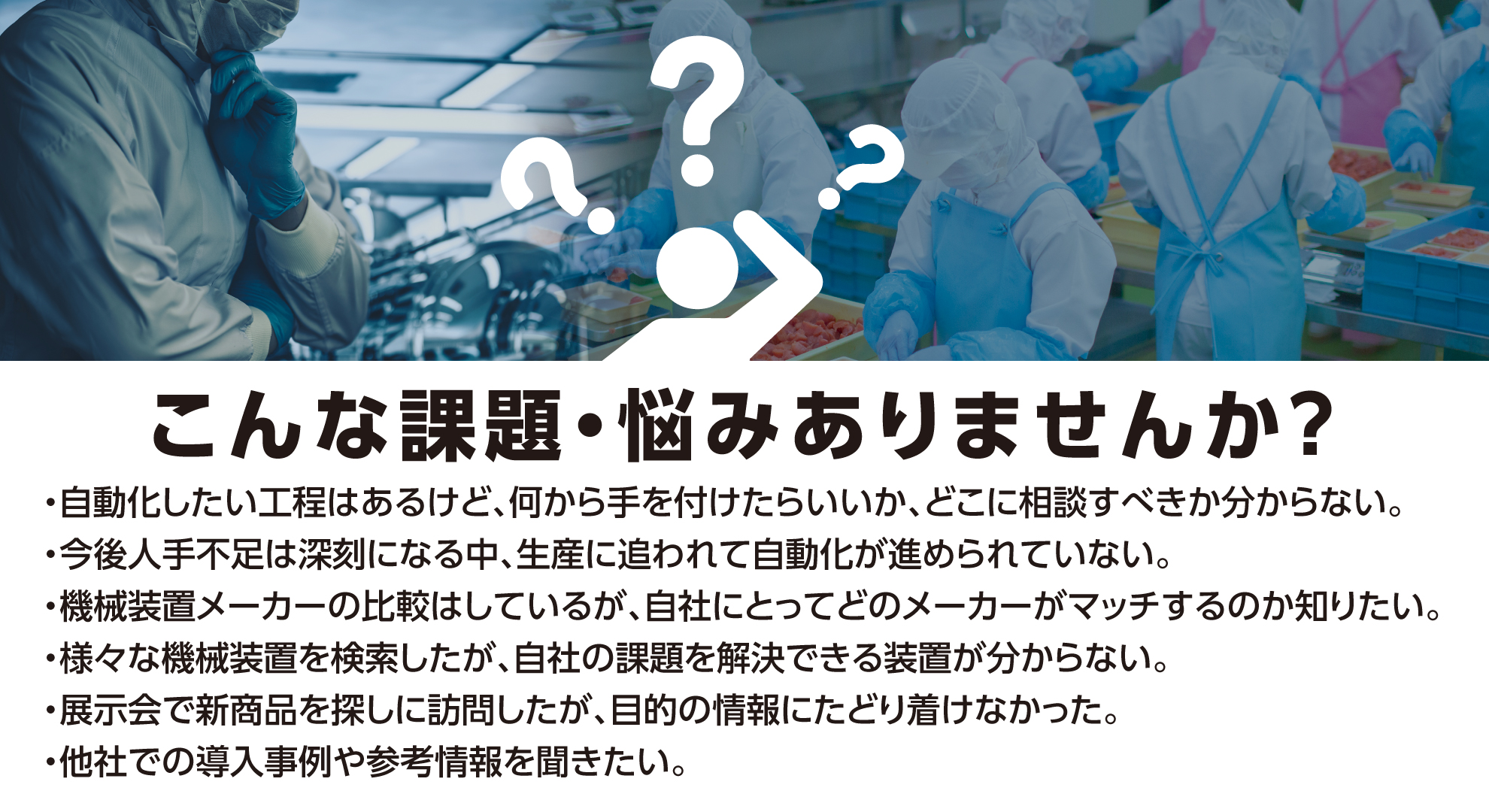

ヒアリングシート
3つのメリットと特徴
-
MERIT 1
- 自動化すべき工程が
明確になる! - 相談は3分で登録完了。自動化したい工程と製造条件を選択するだけ!
- 自動化すべき工程が
-
MERIT 2
- 相談するだけで最適な
メーカー紹介に繋がる! - 1,000社、10,000を超える商品から最適な情報を紹介!
- 相談するだけで最適な
-
MERIT 3
- 補助金や助成金の
情報紹介も可能! - 自動化するために活用できる全国の補助金情報も紹介!
- 補助金や助成金の
物流システムの商品種別から他の解説記事を探す